Aebi Schmidt |Maximum machine uptime and longer service life|Remote Diagnostics
Remote monitoring of machine performance
Remote monitoring continuously checks the condition of machines in the field. This data is made visible in the IntelliOPS platform for fleet and operational management. In addition to information such as the remaining range of the machine, temperature, particulate filter status, number of engine running hours or, for example, battery charge status are transmitted. Any fault messages are transmitted with action advice. Remote diagnosis of any problems reduces the need for physical intervention and saves valuable time. The maintenance party can take action before serious problems arise and unexpectedly higher costs for repairs.
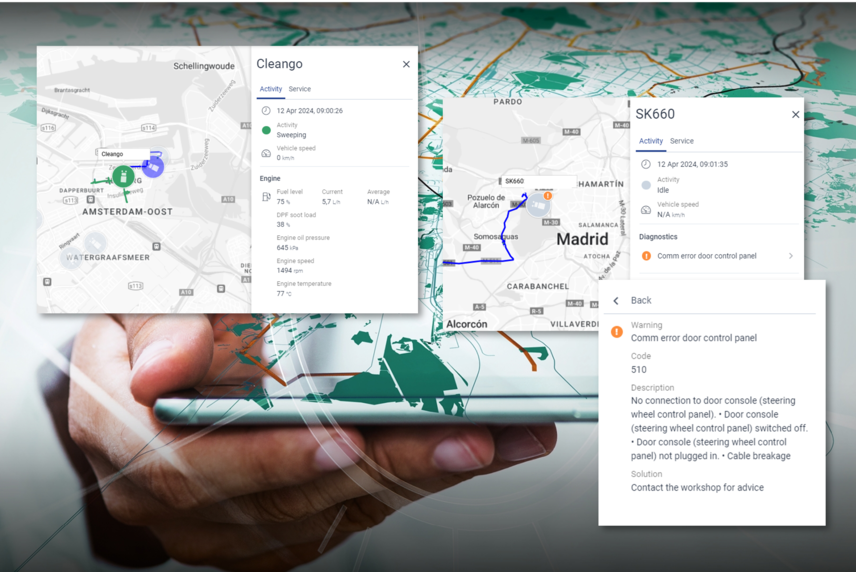
Service planning support
Regular maintenance promotes the optimal performance of machines and extends their lifetime. You or your maintenance partner receive email notifications for upcoming, currently required or missed maintenance. These notifications are based on maintenance messages from the machine itself or on the schedule based on the engine's actual running hours. By having a clear view of the maintenance schedule, optimum use can be made of available workshop capacity and machine uptime. Parts and materials can be ordered in good time. The maintenance planning for different machines is always up to date and is clearly displayed in one platform.
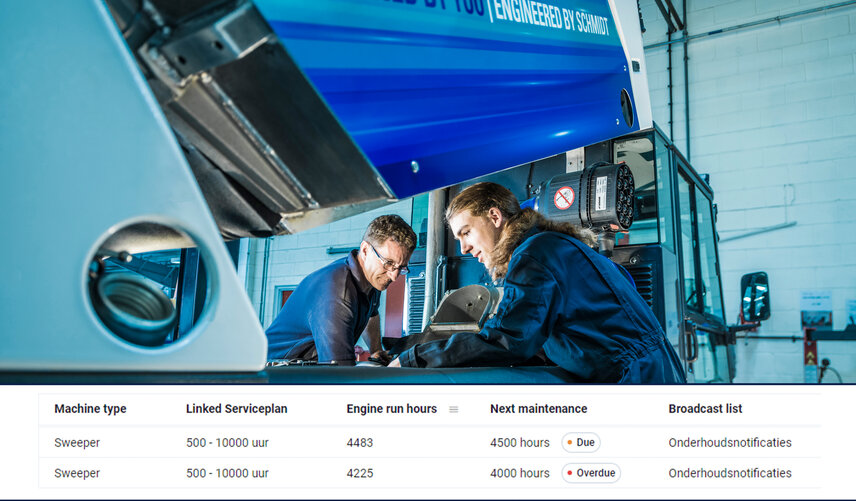