The ‘lean production’ method comes from the Japanese automotive industry. At the end of the 1980s, fluctuations caused by suppliers or customers were dealt with differently in Japan compared to how they were usually dealt with in the USA and Europe at the time. Today, the concept of ‘lean production’ has a permanent place in many industries, and the basic idea has also been incorporated into the methods of many other business processes. Ultimately, it is about automating and designing processes without any interruptions, resulting in savings when it comes to costs, working hours and materials.
It makes bottlenecks and seasonal drops in demand on production islands a thing of the past. By converting to flow production, where the machine is set up to run continuously – without any interruptions and without any interim storage – based on a fixed cycle time, the throughput time per machine can be significantly reduced. And then some. Michael Schneider, Head of Plant in Switzerland, explains, ‘Production management has become more transparent, and planning has become more efficient. These are huge advantages compared to the old method.’
The conversion of the production line drew on valuable experience within the Aebi Schmidt Group, because sweeper production in St. Blasien also follows the ‘lean production’ system. Still, everyone involved had to first be won around to the change and have their doubts dispelled. When asked whether employees are happy with the new production line today, Michael Schneider said, ‘The workstations were adjusted ergonomically and the whole production process is now tidier and clearer, which is great. Commissioning and test runs no longer have to be carried out in the production building forecourt (which wasn’t a very popular option in winter), and there’s now an integrated, stationary test bench where each machine is carefully inspected and parameterised instead.’
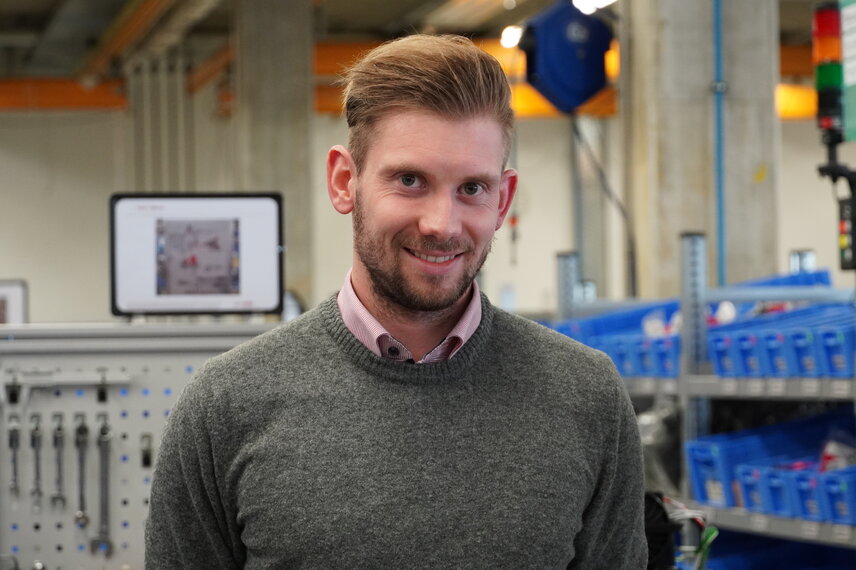
The self-controlled Kanban system on the line also encourages material procurement in a way that saves resources. ‘We are now able to guarantee the continuous improvement process much better than before. We are able to respond to fluctuations in demand immediately and the main thing is we can respond to these using all of our employees. This process used to be a lot more complicated. The flexible capacity works well and, compared to before, twice as many machines can be made using the new method in just one day, if necessary,’ Schneider says proudly.